One of the defining characteristics of warehouse work is the high attrition rates among rank-and-file workers. This has a direct effect on the operational capacity of companies in the logistics industry as was exemplified by Amazon which was said to be running out of people to hire in 2022.
Smart companies realize this and have taken measures to encourage employee retention because it’s good for the long-term success of the business.
As someone who’s worked in multiple warehouses, I’ve seen both sides of the coin – companies that go the extra mile to ensure their workers are well taken care of and those that are totally apathetic towards the plight of their warehouse staff.
Companies whose warehouse workers stick around for a long time have implemented the following strategies:
Create a positive workplace culture
Warehouse employees want to be treated with empathy and respect by both management and peers.
Involving employees in decisions that affect their work is a good way for management to establish a positive working relationship with them.
Great companies ensure that warehouse managers are easily reachable by employees on the warehouse floor e.g., by having an accessible office on the floor as well as easily accessible work phone numbers.
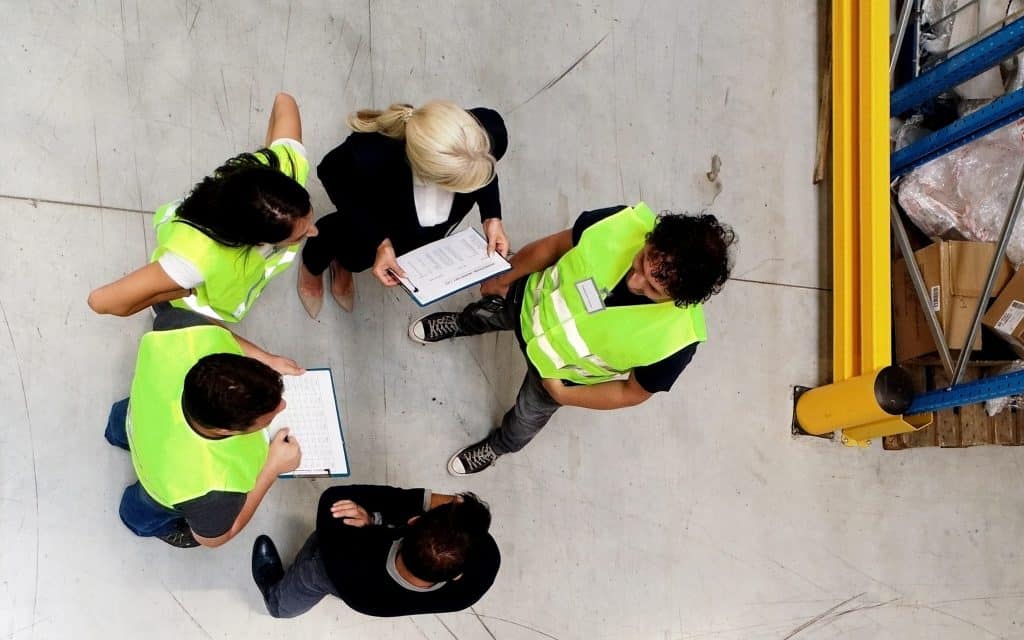
Daily stand-ups are a good way to build cohesion among employees and management.
- With stand-ups, leadership can communicate with employees about goals of the day (e.g., the projected pick quantity) and any news relating to their work or the company that is relevant to them.
- They also serve as a platform for employees to offer suggestions (e.g., when it comes to process flow) and voice their complaints and frustrations to management.
Other social activities like potluck for thanksgiving and lunches or dinners during holidays have a strong impact on team bonding.
A few bad apples can negatively affect the morale of the entire team so those need to be taken care of. Take complaints about colleagues seriously and get rid of repeat offenders or the good workers will leave.
Enact proper health and safety practices
Warehouse employees want to be confident that they’ll get home safely to their families at the end of each work day. This can be done by establishing and following through with good safety practices.
Having a safety committee that is partially composed of low rank employees is a good start. Employees working on the floor know what is going on and will provide much needed insight when they are involved in committee meetings.
Equipment and infrastructure needs to be in good working condition or employees won’t do their work effectively. Slippery floors or worn out forklift forks doesn’t inspire confidence.
Hi-viz vests, work shoes and gloves, harnesses and bibs should be provided for free where applicable. At the very least, have coupons for some of these items.
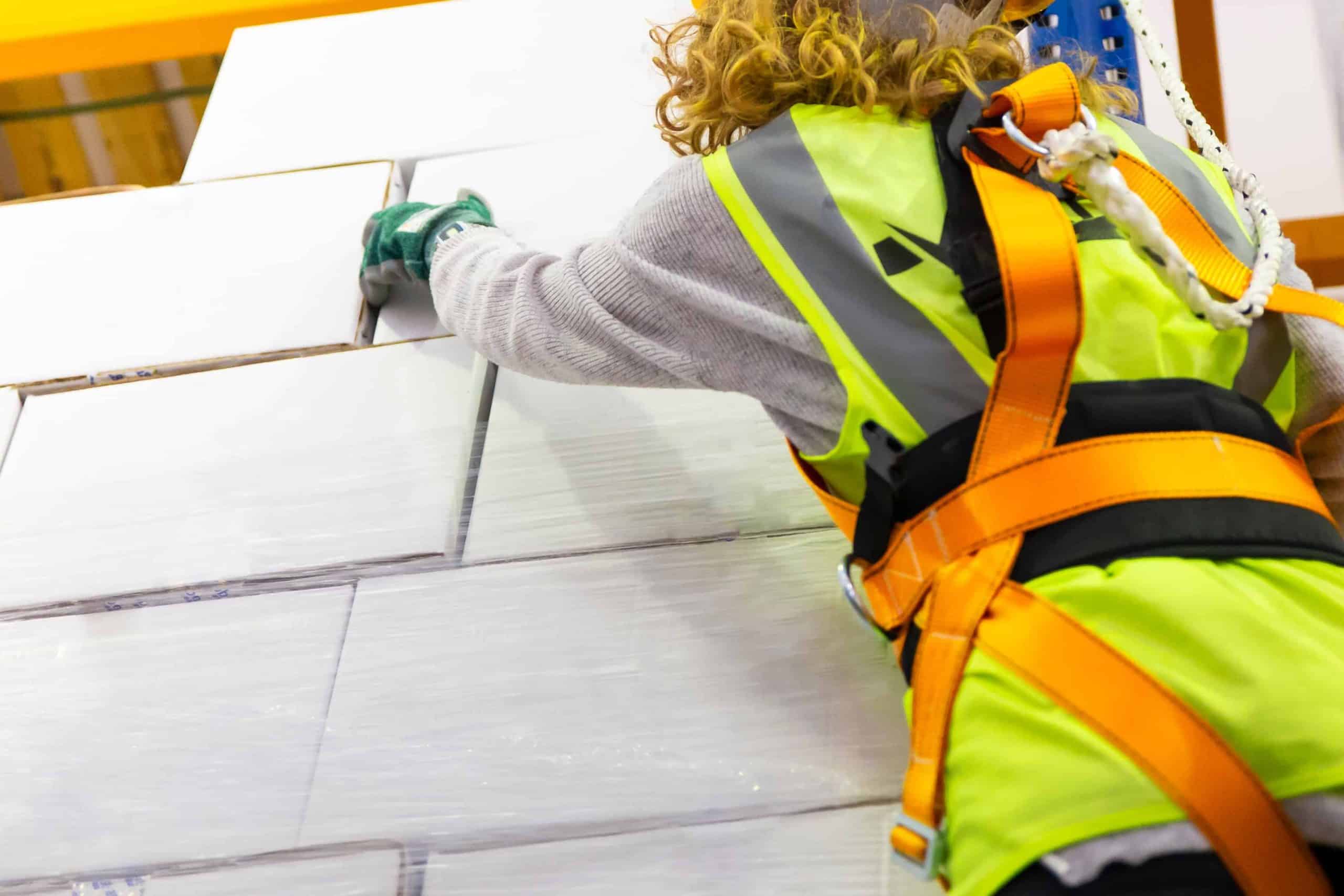
Fit forklifts with collision awareness systems to prevent crashes. Install shock sensors on electric pallet jacks and other powered lift trucks to detect collisions. Employees who cause accidents should be coached and perennial offenders need to be let go as they pose a danger to themselves and their colleagues.
Many warehouse employees deal with mental health issues such as depression for various reasons. An in-house mental-health specialist will help these workers navigate whatever issues they are going through and increase their likelihood of staying. Including mental health in their health insurance benefits also helps.
Injury prevention and management
Soreness and injuries are a fact of life in the warehouse but they can be minimized. Some of the most common types of injuries experienced by warehouse workers include back pain, knee pain, foot pain and carpel tunnel.
Workers who experience chronic pain as a result of their work are more likely to quit. Thus, adequate training, e.g. on proper lifting techniques, is required.
The best warehouse operations have daily stretching sessions before work starts, e.g., during stand-up meetings. Stretching helps prevent musculoskeletal disorders like carpel tunnel and strains.
Having an in-house physiotherapist or chiropractor is convenient and acts as a first-line treatment for minor movement-related injuries. If having an in-house specialist is not feasible, consider having a third party clinic that offers these services near your facility. This also reduces anxiety related to medical costs.
Provide sufficient equipment
There’s nothing more grating to a warehouse employee than finding out that they don’t have forklifts, pallet jacks or ring scanners to use right when work starts. This leads to frustration and lowers morale.
If there isn’t adequate equipment at the beginning of a shift, it pays to let workers know beforehand. This approach will ensure that they are mentally prepared and have enough time to switch to other duties.
Also, ensuring that available equipment is in good working order is important. Disruptions while working due to a pallet jack breaking down or a voice picking headset malfunctioning is going to increase frustration with the job.
Carry out effective training and on-boarding
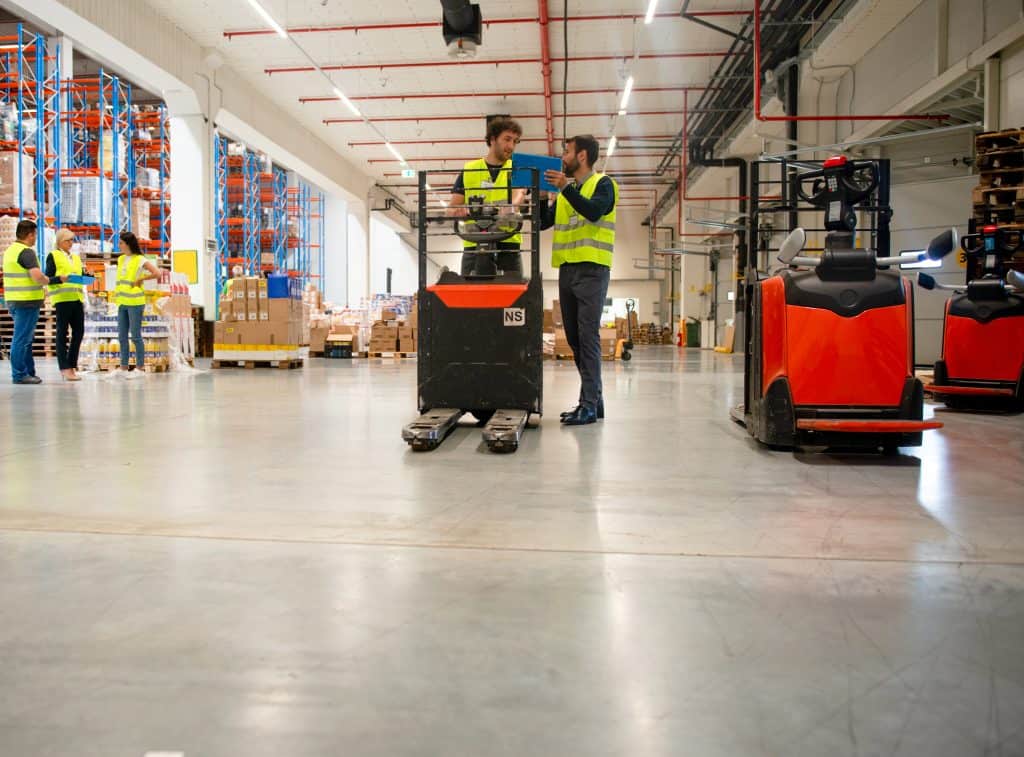
The worst warehouses I have worked at did not give sufficient training to new hires. This meant that the employees were very slow, prone to accidents and slowed down their colleagues.
Poorly trained warehouse workers do not last long. Having regular sit-downs with an employee in the first few weeks (e.g., during probation) about what they are doing right and wrong is a good way to get them up to speed faster.
Hire enough workers
To avoid overworking your employees, put together a sound recruitment strategy that creates a pipeline of new employees streaming in to fill any gaps in productivity.
Pre-employment screening such as background checks is important to ensure every employee is the right fit for the team. You definitely don’t want your warehouse to be described as “they’ll hire anyone with a heartbeat”.
Too much overtime kills employee morale. While there will always be some hourly workers who regularly seek out overtime for the pay, the vast majority will not appreciate it, especially when it’s constant.
Most workers don’t mind overtime if it’s only for a brief period in the year (e.g., during peak seasons). Just notify them beforehand so that they can have enough time to make arrangements with their families.
Promote from within
It’s no secret that entry-level warehouse jobs feel like dead end jobs. To combat this, choose management team members (e.g. leads, supervisors and managers) from among rank-and-file employees and train them for the job. This has a significant impact on their job satisfaction as they are able to see that there are opportunities for moving up.
Managers that have previous hands-on experience on the warehouse floor are also beneficial in other ways:
- They are able to foresee or solve problems that they have encountered before
- They can empathize with their subordinates and be better prepared to handle any issues that affect them
Have acceptable pay and benefits
All measures suggested here won’t matter if employees aren’t paid a living wage, unfortunately. If workers can’t make enough to keep the lights on, they will always have one foot out the door.
Also consider adding bonuses such as profit share and performance incentives as they are known to attract and keep workers.
Benefits should not just cover the employees, but also their families (spouses and children).